Kitplane
Transport
or
Jed Clampett meets Vans Aircraft
I’ve had to do a complete cross country
kitplane transport
twice.
I guess that’s one of the hazards of being in the military.
Here's how I did it.
I started
building while I was
stationed in North Carolina. While I was there, I finished
the
tail and wing kits, and started on the fuselage. I had
everything
drilled on the jig, but only the floor skeleton and bulkheads
riveted. So when it was moving time, everything laid pretty
flat.
First
move: North Carolina to Pensacola
I
kept the crates Vans shipped everything in and used them for my first
kitplane transport. The vertical stab, rudder, elevators,
flaps and
ailerons
all fit into the crate Vans shipped the wing kit in. I used
old
blankets for padding between the parts.
The
wings fit
into the crate from the fuselage kit. I had some one-inch
Styrofoam that I put in first, then the two wings. I screwed
a
block of wood to the end of the crate, and clamped the spars to
it. Then I bolted some small blocks through the lightening
holes
on the tips. Another piece of one-inch Styrofoam and I put
the
top on.
Hurricane
Ivan
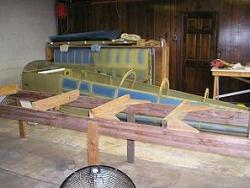 You
can see the wings
still in the crate in
my first
shop in Pensacola. This was before Hurricane Ivan wrecked
it. Actually, Ivan trashed everything around my shop, but
left it
standing -- leaking, but standing. The rooms on either side
were
completely destroyed and their ceilings caved in. The entire
front half of the hanger was gone, you can see the bent rafters lying
on the concrete. The remains of the T-hangers are on either
side
of what’s left of my hanger.
Second
Move: Pensacola to Louisiana (2006)
My
second kitplane transport was a little more difficult. By
this time the plane took
up
a lot of space. Again, everything went into the crates, then
I
packed everything (plus my completed kit
motorcycle project)
onto a
trailer for carrying cars. The crate with the empennage went
on
the bottom, between the tracks a car would normally drive on.
The
wings went on next, and the fuselage topped it off. That’s my
toolbox and engine on the front. You can just see the front
tire
of my bike poking out. The small fuselage kit crate was
behind
it. If you look real close, you can see the horizontal stab,
wrapped in foam and tucked under the wing crate. The entire
kit,
plus my bike, fit on the trailer.
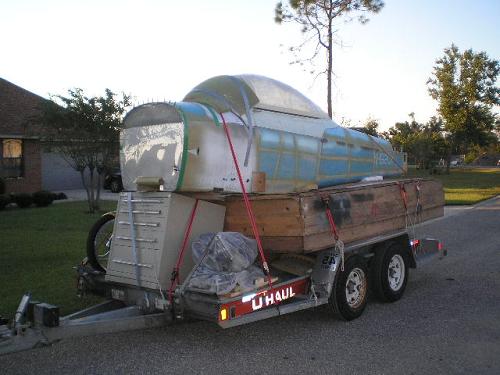
I can hear
the banjo.
"Y'all come back now, ya hear?"
Third Move: Louisiana to North Carolina (2009) It was time to move again, and the
engine wasn’t running smoothly. So I had the choice of working
feverishly and hoping I found the problem, or knocking-it-off,
pulling the wings, and trailering the plane to our new home. I opted
to trailer the plan. My wife noticed that when I have a deadline,
building the plane becomes too much like a job, and less like fun.
Plus I didn’t want to get rushed and make a stupid (fatal) mistake.
So I spent a few days at the airport
getting ready for my third, and hopefully last, kitplane transport.
I removing the ailerons, flaps, wings, and prop. I put the
ailerons,
flaps and wingtips in the smaller crate on the trailer. The wings
went back into the large crate. But this time, the pitot tube was
installed and made the wing too fat to fit in the crate. Instead of
unriveting the pitot tube, I opted to cut a hole in the top of the
crate. Then I wrapped the pitot tube with plastic and covered that
with tape. I made some foam covers to fill the holes in the cowling,
and covered the canopy with plastic and foam. I started by washing
the canopy real well, and then covered it with plastic wrap. Finally
I taped foam on top of all that. I figured the plastic wrap would
protect the canopy from getting rubbed and scratched by the foam, and
the foam would protect it from rocks on the trip.
You can see on the tail the “keeper”
I made to hold the rudder in the streamlined position. I copied
this idea from the “donuts” we used on some of the jets I have
flown. I cut two pieces of plywood into about 8 inch squares. Then
I cut two pieces of soft foam to match, and drilled a hole through
the center of all four pieces. I used a piece of threaded rod, nuts
and washers to hold it all together. I put a washer and nut on one
end of the threaded rod, then slipped the plywood and then foam on.
I then pushed the threaded rod through the space between the rudder
and the vertical stab. It only fits in the lower leading corner of
the rudder, I can’t slip it up and out between the rudder and stab.
Then on the other side of the stab, I put foam, plywood, washer and
nut onto the threaded rod. I tightened the whole thing by just
squeezing the entire assembly with one hand and tightening the nut
with the other, no tools required.
I also made one of these for the
elevators. It fits in the aft corner of the horizontal stab, between
the stab and the elevator.
Everything made the trip with no
problems. The hardest part of this kitplane transport was removing the duct tape residue from
the sides of the plane when the move was complete. 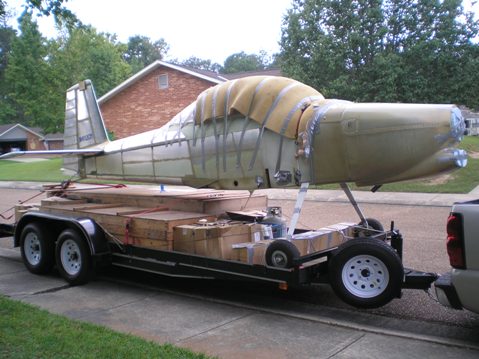
Final Move? Hopefully
this really is the last
ground move for the plane. I really want to fly it to the next
destination. It's late 2009, and as soon as I get the engine
running properly, I'll be flying. No more kitplane transport for
me! Through all three
moves, packing up
for four hurricanes, and actually getting hit by one, the parts have
all made it fine. Van’s crates worked perfectly.
Return
from Kitplane Transport
to Tools and Tips
Return
from Kitplane Transport
to Kit Plane Advice Home
|