Fitting the Plexiglass Bubble
For me, fitting the plexiglass bubble to my
airplane was about removing the extra forming material, cutting the
bubble and polishing the edges, and drilling holes.
I had problems with the last step. Here's how I did
it.
Removing
Extra Material
I started
fitting the plexiglass bubble by
removing all of
the extra lip left from forming. Then
for each successive cut I removed only ¼” at a time. It took
a lot of cuts, but I was certain I
wouldn’t remove too much material this way. I initially
removed front and back material, and
eventually started on
the sides too. I
used a cutoff wheel and
scotchbrite pad on the angle grinder for all the straight cuts, and my
Dremel
tool with a sanding disk for the notches.
I found drawing some
centerlines
helped with the progressive
fittings. I made a
line 3 ¼” aft of the
F-866B bulkhead with a mark on the center of the front skin. Then I made a
corresponding line on the
center of the front of the canopy bubble.
I also made a line on the aft center of the
bubble. I didn’t
need an aft
centerline on the
fuselage; I just used the rail to center the line.
These lines helped me set the canopy at the
same spot every time I fit it to the frame.
I almost removed too much
from the
front. I was
surprised by how much the front was
lifted up when I pulled the sides in to touch the rails. But because I had taken it
slow and only
removed a little at a time, My final gap at the front was only 1/8 inch.
Cutting
the Plexiglass Bubble
I cut the bubble in two
just like the
directions say, using
a piece of cardboard as a guide. It
worked perfectly.
After the cut, I polished
all the
edges completely smooth
using progressively finer scotchbrite wheels and finished with
sandpaper. I have
an almost clear finish on the edges of
the plexiglass bubble. This
may be a little
much, but I didn’t want to leave a scratch or tool mark that could
later turn
into a stress point and crack.
Drilling
the
Holes
The special plexiglass
bits that I
bought didn’t look like
the ones I was used to. They
didn’t have
the tapered tip that I am familiar with, like the one shown in this
picture
from AC 41-13b.
I asked and the supplier
said they
were the right bits, and
even sent me another set just to be certain, but they looked just like
the
first ones. Still
skeptical, I tried
them on a piece of scrap plexiglass, and it drilled without cracking. So I took the plunge and
drilled the first
hole in the canopy – it cracked! I
was
pissed, but what to do now? I
threw away
these bits and got some that I was used to, and drilled all the other
holes.
Luckily
the first hole was in
the forward leading edge of the canopy where it will be below the
fiberglass
seam. I planned on
putting a thin layer
of fiberglass there and painting it anyway, so this would cover the bad
hole. I “fixed” the
hole by drilling it larger with
a good bit until all the cracks were removed.
Once I applied the thin
strip of
fiberglass, the repair was
covered, and final painting will do the trick.
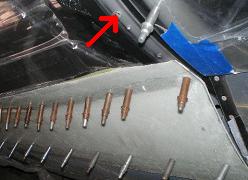
I drilled the frame
according to the
spacing in the plans,
but then ended up with way too many holes and not near enough CS4-4
rivets. The plans
call for 1 15/16” spacing all the
way around the frame, for 44 holes total.
I ended up with way more than 44 holes, and
only 40
something CS4-4s. So
I called Vans and told them about the discrepancy
and asked which way was it supposed to be?
They saw the problem, and said they would look
into fixing
the plans,
and they sent me a bunch more CS4-4s.
So
I had enough rivets to install one in every hole.
Now let's move to the
next step of the canopy assembly process by working on the canopy
skirt.
Return
from Fitting the
Plexiglass Bubble to Finishing
Kit
Return
from Fitting the Plexiglass Bubble
to Kit Plane Advice Home
|